Behind the Scenes: The Technology of Custom Printed Patches
- Jonathan Swift
- Oct 24, 2024
- 2 min read
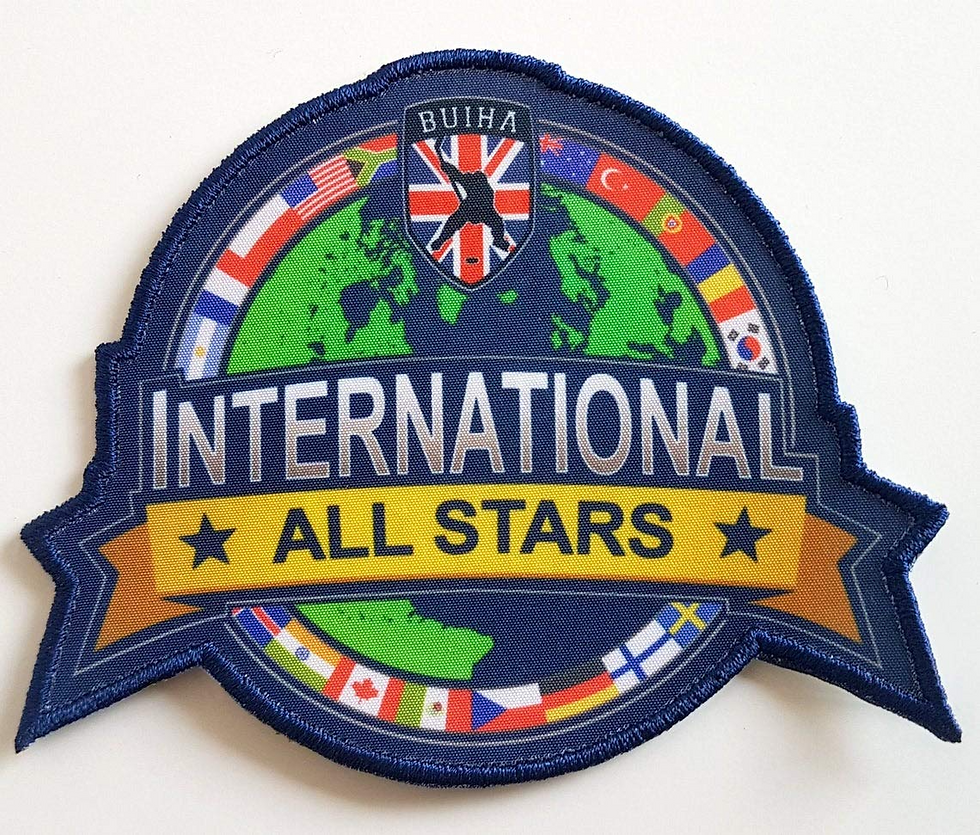
Custom patches are not just accessories for the eyes. They are essential tools for storytelling, brand identity, and self-expression. Custom hat patches and custom printed patches hold an exclusive position in the craft and design industry, being used by everything from army units to fashion enterprises and even potters. What steps are involved in turning an idea into an embroidered patch? Every patch is a work of art, combining creativity, technology, and expertise from conception to design. On this topic, we'll look at the process of creating unique patches, exploring every stage from the initial idea in the morning to the finished embroidery.
1. Developing the Design Concept
Imagining the idea is the first step in creating the personalized patch. At that point, creativity is at its height. Regardless of whether you are a developer, owner, or someone looking to communicate directly with others, a thorough understanding is the first step in the design process. In what way do you envision your patch representing? What message or concept should it convey?
A variety of sources, such as pop culture, nature art, and personal experiences, can serve as inspiration for the brainstorming and alleviating process. Documents and sketches must be gathered in order to profit from the idea's fantasy.
Selecting Colors and Shapes
Colors have a significant role in design. They evoke emotions and give the custom patches a vibrant appearance.
2. Producing the Digital Layout
Applying the concept through digital design will be the next stage after it has been defined. This is the process of rewording the idea so that it may be produced as needlework.
Conversion of Vectors
Vector plate applications, which are comparable to Adobe Illustrator, are typically used to create the design. To ensure that the design can be measured without sacrificing quality, vector plates are essential. Vector plates are appropriate for embroidery because of their precise details and clean lines.
Line Data Formats
Depending on the embroidery machine, the finalized design is saved in specific formats, such as DST, PES, or EMB.
3. Selecting Vestments and Accessories
When creating patches, selecting the right accessories is crucial. The final product's feel and appearance will be greatly influenced by the choice of backing, fabric, and thread.
Selection of Fabrics
The most popular materials for custom printed patches, including custom hat patches, are polyester, twill, and felt. The cloth should be suitable for the patch's intended use and durable enough to withstand the stitching process.
Thread Types
High-end embroidery vestments are typically made of rayon or polyester and are selected based on their colorfastness, strength, and sheen.
4. Embroidery Items
The patch is now prepared for product placement following the digitization of the design and the naming of the accessories. This is the point at which technology and artistic creation combine to create the finished product.
Taking Care of
The design is sewn onto fabric by a machine. Depending on the size of the pattern, the process could take several minutes to several hours. An embroidery machine with numerous heads may produce multiple patches at the same time.
Control of Quality
After the needlework is finished, the patch is inspected for errors or grammatical infractions. To prevent fraying, loose garments are cut, and patch edges are trimmed.
コメント